光造形法
光造形は、代表的な3次元造形法の一つであり、ラピッドプロトタイピング技術の先駆けの造形手法です。原理的な技術は1980年に日本人が発明し、その後アメリカで1986年に製品化されました。日本ではラピッドプロトタイピングとして導入されている装置の半分以上がこの光造形法を利用した装置です。
液状の光硬化性樹脂で満たした水槽に紫外線を照射すると、照射された部分が光重合反応を起こし硬化します。硬化させた層を積み重ねて、造形を行います。
ラピッドプロトタイピングの手法の中でも、細かな造形や正確なサイズ表現に優れています。
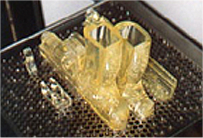
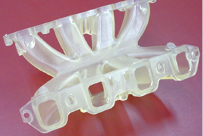

②普及している工場が多い
③造形物の長期利用は困難
成形物は光硬化性の樹脂でできており、太陽光などと反応し、変質していきますので、長期間の公差の維持には向きません。
また、光造形に用いることのできる樹脂はエポキシ樹脂のみであり、ABS樹脂等に比較すると、単価は高い物になります。特に大物になると、材料及び造形時間が長時間になってしまうため、外注に出す場合は、料金に注意する必要があります。
一般的には、単品の部品試作に向いている手法と言えるでしょう。
未だ開発段階ではありますが、積層造形法の発展形として、任意面積層法という手法も考案されており、今後造形時間が更に短くなる可能性もあります。
試作手法の概念図
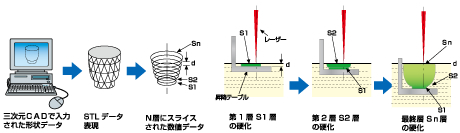
光造形の造形プロセスを簡潔に説明すると、光造形とは一層分の形状データに紫外線レーザーを照射して硬化させ、一層分を下降させ次の層を硬化させる、という動作を繰り返して形状を作り上げる方法です。積層造形法では1層あたりの高さを低く制御することで、表面精度を向上させることができますが、光造形は0.2~0.05mm程度の層厚さで造形が可能です。
この精度は樹脂の収縮、レーザー波長とも関係しますが、現時点で光造形はインクジェット方式、切削方式と並んで製作品精度においてトップクラスを誇る手法です。
なお、造形物は液体内に硬化物として造形されるため、傾斜部分には造形物を支える「サポート」と呼ばれる部分が必要です。このサポートは造形終了後には不要部分であり、除去する必要があります。
主要メーカーとして、海外であれば3DSystem社、国内では、シーメットなどがあり、開発が盛んです。
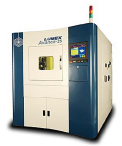
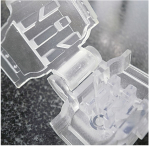
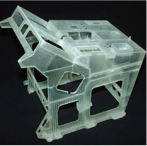